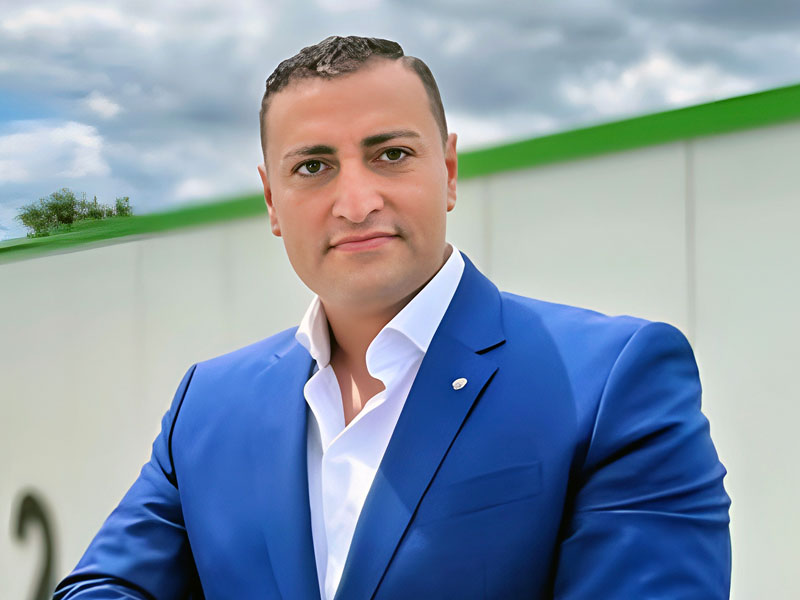
Recently, consumers have become increasingly aware of the environmental impacts of their purchasing decisions, leading them to seek sustainably produced and packaged products that minimise their ecological footprint. PAPACKS recognised this growing trend a decade ago, which has greatly influenced our packaging design and prompted us to invest extensively in the research and development of manufacturing processes and sustainable materials. These materials are easy to recycle or compost and minimise waste.
PAPACKS is now a leading manufacturer of molded fibre packaging solutions, setting the standard in Europe for sustainable, fibre-based packaging. With production capacities of over 600 million units annually, we are leaders in both production volume and innovation, boasting an impressive array of over 75 patent families, 30 awards, and more than ten years of continuous development and research. With a focus on climate protection and the conservation of natural resources, we emphasise the use of renewable raw materials and production processes, especially virgin fibres and industrial hemp. This approach enables us to make a significant contribution to reducing the CO₂ footprint, offering tangible benefits to clients and the environment alike.
Packaging for tomorrow
Future packaging will be more eco-friendly, lighter, more efficient, and driven by technological advancements. While smart packaging and the Internet of Things (IoT) offer enormous potential, enabling packaging to be equipped with sensors and other technologies to provide information about the product’s condition, origin, and shelf life. The question remains, how often consumers will actually scan packaging with an RFID chip or QR code to find this out. The best approach is to create packaging from materials that clearly indicate they are sustainable, can be reintegrated into existing waste paper cycles, and are easily compostable.
At PAPACKS, we use molded fibre packaging that utilises renewable materials such as tree fibers and hemp fibres. Our goal is to replace simple plastic and EPS transport packaging while also developing complex products like plastic bottles and other containers and packaging products. We are also exploring and developing intelligent packaging solutions and believe these technologies will allow us to create even more sustainable and efficient packaging that simultaneously adds value for our customers by enabling them to verify the true sustainability of the packaging and therefore avoiding misleading advertising claims.
Circular design
Applying the principles of circular design, which considers all phases of the packaging lifecycle from design and production to use and disposal, a key aspect is selecting appropriate raw materials that minimise the packaging’s ecological footprint. Our molded fiber technology is not only more sustainable than traditional packaging materials like plastic, glass, EPS, or aluminum, but can also be easily recycled or composted, thus closing the packaging lifecycle and fulfilling the circular design principle. We are continuously working on developing and optimising our packaging to further reduce its ecological footprint and meet the requirements of a circular economy.
PAPACKS has planted more than 2,000 hectares of the more efficient raw material industrial hemp in Ukraine
Companies can use specialised software tools and databases to collect and analyse the environmental impacts of their packaging throughout its entire lifecycle, considering various indicators such as energy consumption, water usage, greenhouse gas emissions, and waste generation. The results enable them to understand the impacts and identify opportunities for improvement. Various strategies can also be used to reduce their packaging’s carbon footprint, including switching to sustainable materials, optimising transportation routes, sourcing local materials and products, and improving the packaging’s entire lifecycle. PAPACKS focuses mainly on production in Germany and Europe, but offers a licensing model for interested parties to build their own local production facilities with our know-how and technology, which helps keep everything local and further reduces the carbon footprint.
Challenges and opportunities
There are several challenges for any organisation implementing a circular design. However, we see it not only as an ethical obligation but also as a business opportunity. By focusing on sustainable packaging, we can differentiate ourselves as market leaders. At PAPACKS, for instance, we have successfully converted many customers from plastic inlays to fibre molds, improving packaging aesthetics and leading to higher sales as more end consumers pay attention to product packaging. Other examples of our successful circular design initiatives include our ICEBOX concept, which can replace EPS boxes for seafood transport, and our advent calendar inlays and overall concepts for saving plastic thermoformed inlays.
This demonstrates that circular design and sustainable packaging are not only ecologically sensible but also economically viable. These are just a few products among some of our highlights in development and production. These include paper bottles and containers made entirely from tree or hemp fibres, Refill caps for the cosmetics industry, food trays for the food industry, and much more. This will enable us to completely replace plastic and other resource-limited products in the future.
Replacing plastic
While there are no actual obstacles to the widespread adoption of non-plastic packaging materials, the real challenge lies in developing a complete set of standards that do not exist in some areas. They often depend on the specific requirements of the customer and products to ensure that sustainable packaging offers similar performance to plastic.
Molded fibres
Biodegradable and compostable materials will play a crucial role in the future of packaging, as they offer sustainable alternatives that do not cause significant environmental problems. While biodegradable materials are designed to be broken down by naturally occurring microorganisms, compostable materials go a step further and can be fully converted into compost under specific conditions. They are particularly useful for food packaging, as they can be composted along with all food waste.
Among the various available alternatives, molded pulp from renewable materials like cellulose fibres or hemp fibres offers a simple, efficient, and sustainable solution. It enables the production of purely natural packaging that integrates easily into existing waste paper recycling cycles or new circular systems.
While today they are molded by modern machines, the technology has existed for over 100 years and enables the production of the purest natural packaging product, which can also be integrated into the existing waste paper recycling cycle. Compared to paper production, which requires high energy and production efforts, the manufacturing of molded fibres is more efficient and environmentally friendly.
The molded fibre industry
In response to the growing demand for sustainable packaging, the molded fibre industry is investing in new technologies and product developments. Although the industry is slowly expanding into untapped markets and new products, the market is already worth nearly $4.3bn, with demand increasing annually to nearly 12 million tons by 2023.
Compared to traditional packaging materials, molded fibre can be very competitive in terms of cost and performance. In some cases, it can offer better protection, durability, and user-friendliness and even be more cost-effective, especially when considering the environmental costs of conventional materials. Molded fibre packaging also offers excellent shock absorption, is lightweight, can be produced in many shapes and sizes, and has the added benefit of being eco-friendly, biodegradable, and often compostable.
molded pulp from renewable materials like cellulose fibres or hemp fibres offers a simple, efficient, and sustainable solution
At PAPACKS, we use tree or hemp fibres for our molded fibre technology, both of which are compostable after use. Our virgin fibre is a white, fresh fibre made from tree cellulose sourced from sustainably managed forests and ready for use in the circular economy. While it offers high quality and performance, the process of producing tree fibres is resource-intensive. In contrast, our industrial hemp is a highly sustainable material that places hemp at the heart of innovative packaging. In terms of sustainability and performance, hemp fibres are comparable to tree fibres, but hemp grows much faster than trees, meaning it can be harvested within a few months, allowing for much faster regeneration and availability of the raw material. Moreover, hemp consumes significantly less water than trees, making it an efficient choice in water-scarce regions, and hemp is an excellent CO₂ absorber, capturing four times more CO₂ during its growth phase than trees. This provides companies with a significant advantage to physically offset their CO₂ emissions with its packaging in the future.
It’s no surprise that the food industry is leading the way in adopting molded fibre packaging, accounting for two-thirds of the total volume. As we are BRCGS (Brand Reputation through Compliance Global Standard) certified, we consider this sector particularly relevant and important for our activities, and the possibilities for using our molded fibre products are diverse. We are also active in the cosmetics industry, where thermoformed molded fibre packaging with high-quality surfaces is becoming increasingly popular. Also, in the logistics and shipping industry, where our packaging serves as a sustainable alternative to present and protect products.
Avoiding rising costs and shortages
The packaging industry is already experiencing shortages of virgin fibre raw materials, and if everyone switches to paper-like packaging, these raw materials will become scarcer in the future, which means their prices will rise. This will then impact production costs, which are typically passed on to customers, leading to higher prices for end consumers as companies try to offset the increased costs. This can be particularly challenging in industries where profit margins are already thin.
the molded fibre industry is investing in new technologies and product developments
To be prepared for future cost increases due to shortages, PAPACKS has planted more than 2,000 hectares of the more efficient raw material industrial hemp in Ukraine with its strategic partner, the European Material Bank. This enables us to independently supply ourselves with high-quality virgin fibre, regardless of what happens in the market.
The economic impact of investing in the packaging of the future is significant, and any company that does not invest will fall behind. In an ever-evolving world, new, modern, sustainable, and truly transformative packaging that solves our plastic and waste problems will quickly find its way, prevail, and be used industrially.
I am also the president of the European Moulded Pulp Producer Association (EMPPA), which we founded to bring together the entire molded pulp industry and encourage and support the still small industry to move in the right direction. Our goal is to advance innovation in the packaging industry and inform politically at all levels about what is feasible to accelerate upcoming laws, such as the EPS ban. By investing in sustainable packaging technologies, we can pave the way for a packaging industry that works for our planet and not just for the marketing of the companies that use these packages.
More information: www.papacks.com